Aluminum Casting Demystified: Secret Methods for Success
Aluminum Casting Demystified: Secret Methods for Success
Blog Article
Dive Into the Globe of Light Weight Aluminum Casting: Understanding the Various Techniques
Aluminum casting is a basic procedure in the manufacturing sector, with different techniques employed to develop specific and complex elements. Understanding the various techniques made use of in light weight aluminum casting can supply important insights right into the capabilities and constraints of each method. From the traditional sand spreading method to the innovative die casting procedure, each method supplies distinct benefits depending upon the needs of the job. Discovering these diverse approaches can provide a comprehensive view of the opportunities within the world of light weight aluminum casting and exactly how each technique contributes to forming the contemporary manufacturing landscape.
Sand Casting Technique
Sand spreading, a widely-used approach in aluminum spreading procedures, involves producing mold and mildews constructed from compressed sand for pouring liquified steel. This method is economical and highly versatile, making it a prominent option for different sectors. The procedure begins with the creation of a pattern, usually constructed from timber or steel, which is then pressed into the sand to leave a perception. The sand blend, normally silica sand blended with a binder like clay, is firmly packed around the pattern to develop a mold tooth cavity. When the mold is all set, it is firmly put in a flask and molten light weight aluminum is put into the dental caries.
After the metal has actually cooled down and solidified, the sand mold is escaped to reveal the light weight aluminum spreading. Sand casting allows for the production of intricate forms and big parts that may be hard or pricey to produce making use of other techniques. It is likewise a sustainable strategy as the sand can be recycled and used several times, lowering waste in the casting process.
Irreversible Mold Strategy
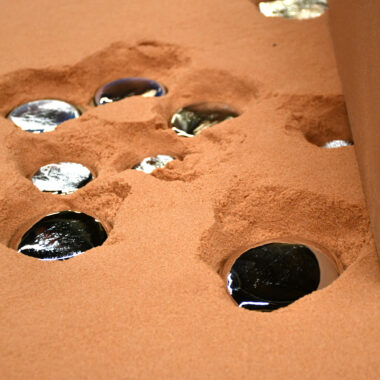
One substantial benefit of the Irreversible Mold And Mildew Strategy is the enhanced dimensional precision it uses. The metal mold permits tighter tolerances and finer information in the last light weight aluminum spreadings compared to sand casting methods. This precision makes it a preferred choice for applications where limited dimensional control is critical, such as in the auto and aerospace sectors.

Die Casting Process
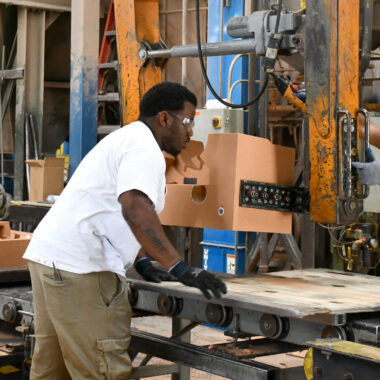
Financial Investment Casting Technique
Using an accuracy spreading technique, Investment Casting Strategy includes creating detailed aluminum components by putting molten steel into a ceramic mold and mildew. This procedure, also recognized as lost-wax casting, starts with the development of a wax pattern of the desired component (aluminum casting).
The next action involves putting the molten light weight aluminum into the ceramic mold and mildew. The aluminum loads the tooth cavity left by the wax pattern, taking its form exactly. This approach is favored for its capacity to create intricate shapes with high precision and a smooth surface coating. Investment spreading is generally utilized for manufacturing elements in sectors where tight resistances and intricate styles are called for, such as aerospace, automobile, and clinical equipment. The adaptability and precision of the Investment Casting Strategy make it an important strategy on the planet of aluminum spreading.
Lost Foam Spreading Technique
Having actually discovered the intricate precision of Investment Casting Method, the focus now moves to the ingenious approach of Lost Foam Spreading in light weight aluminum part production. Lost Foam Spreading, additionally recognized as evaporative pattern spreading, is a modern-day strategy where a foam pattern of the desired component is developed and after that covered with a refractory product. The layered foam pattern is after that buried in sand, and molten aluminum is poured right into the mold and mildew. As the steel loads the mold and mildew, the foam vaporizes because of the warm, leaving a clean cavity in the shape of the wanted component.
One of the main benefits of Lost Foam Spreading is its capability to produce intricate forms with complex details, often in a solitary item without the find need for additional machining. This approach is likewise known for its high dimensional precision and smooth surface coating. Furthermore, Lost Foam Casting is a cost-effective procedure as it decreases the need for cores and enables the production of lightweight parts. In spite of its benefits, Lost Foam Casting requires cautious control of the casting procedure to avoid issues and make sure top quality elements.
Final Thought
To conclude, aluminum spreading supplies a variety of techniques such as sand spreading, permanent mold method, pass away casting, investment casting, and shed foam spreading. Each method has its own advantages and applications, making light weight aluminum casting a Website functional and widely utilized process in numerous sectors. Understanding the differences between these techniques is vital in choosing one of the most ideal spreading technique for certain manufacturing needs.
Sand spreading, a widely-used approach in light weight aluminum spreading procedures, involves developing mold and mildews made of compressed sand for pouring molten metal. aluminum casting.The Permanent Mold And Mildew Strategy, like sand spreading, is an additional prevalent method employed in aluminum spreading processes, providing distinct advantages in terms of mold reusability and dimensional accuracy. The metal mold and mildew allows for tighter tolerances and better information in the last light weight aluminum spreadings contrasted to sand casting methods. The two primary types of die casting are cold chamber pass away spreading and warm chamber pass away spreading, each ideal for various types of aluminum alloys.In conclusion, light weight aluminum spreading uses a range of techniques such as sand casting, permanent mold and mildew technique, die spreading, financial investment casting, and lost foam spreading
Report this page